SUCCESS STORY
Modernising Field Service and Warehouse Management
Kagool updated Cadent's Warehouse Management system, enabling field engineers to quickly order the parts they need to efficiently carry out their jobs, while simultaneously keeping stock level information easily accessible and always up to date.
Cadent Gas
Cadent is one of the largest gas suppliers in the UK, delivering gas to 11 million residential and business customers. Employing over 4000 people in the UK, they are responsible for the maintenance of 82,000 miles of gas pipes.
They deploy field engineers to repair and replace the gas pipeline as required, both proactively and reactively, ensuring safe and reliable provision of gas across the country.
The Challenge
Cadent has a National Distribution Centre, which acts as the company’s central nervous system. Beyond this, there are 18 secondary and 38 tertiary parts stores across the UK. From these stores, field engineers pick up parts they need to repair the gas network and carry out new installations.
The National Distribution Centre was running on SAP, but none of the other stores had full SAP capabilities. Instead of using SAP throughout the whole of business, there was a reliance on large volumes of manual data entry – approximately 2 million entries per year, many of these being paper based. This led to multiple inefficiencies with increased costs, where tracking orders and stock levels was a major challenge.
These challenges led to significant efforts being required simply for basic warehousing operations, and there were often delays in these processes.
The client had SAP Extended Warehouse Management (EWM) Licenses already, but they were not being used.
Our Solution
Kagool carefully defined all the business requirements for a potential solution, before laying out a plan based on SAP EWM. The solution was designed and delivered with standard SAP EWM functionality, reducing costs and complications for the client.
Kagool set up and configured
SAP EWM
to deliver Cadent Gas Warehouse Processes, and were responsible for
data migration from Cadent Gas legacy systems.
The new system is paperless, and many tasks such as printing labels have been automated. Kagool also went above and beyond the initially defined business requirements in order to integrate the solution with a new barcode scanning system.
Finally, Kagool developed a
mobile app on Fiori which field engineers will use to order parts to their preferred delivery stores. The system will automatically update
stock level information based on these orders.
The solution was rolled out successfully with emphasis on testing, including all exception handling scenarios. Kagool deployed the solution according to a plan which strategically balanced business risk with efficiency of delivery.
Outcomes
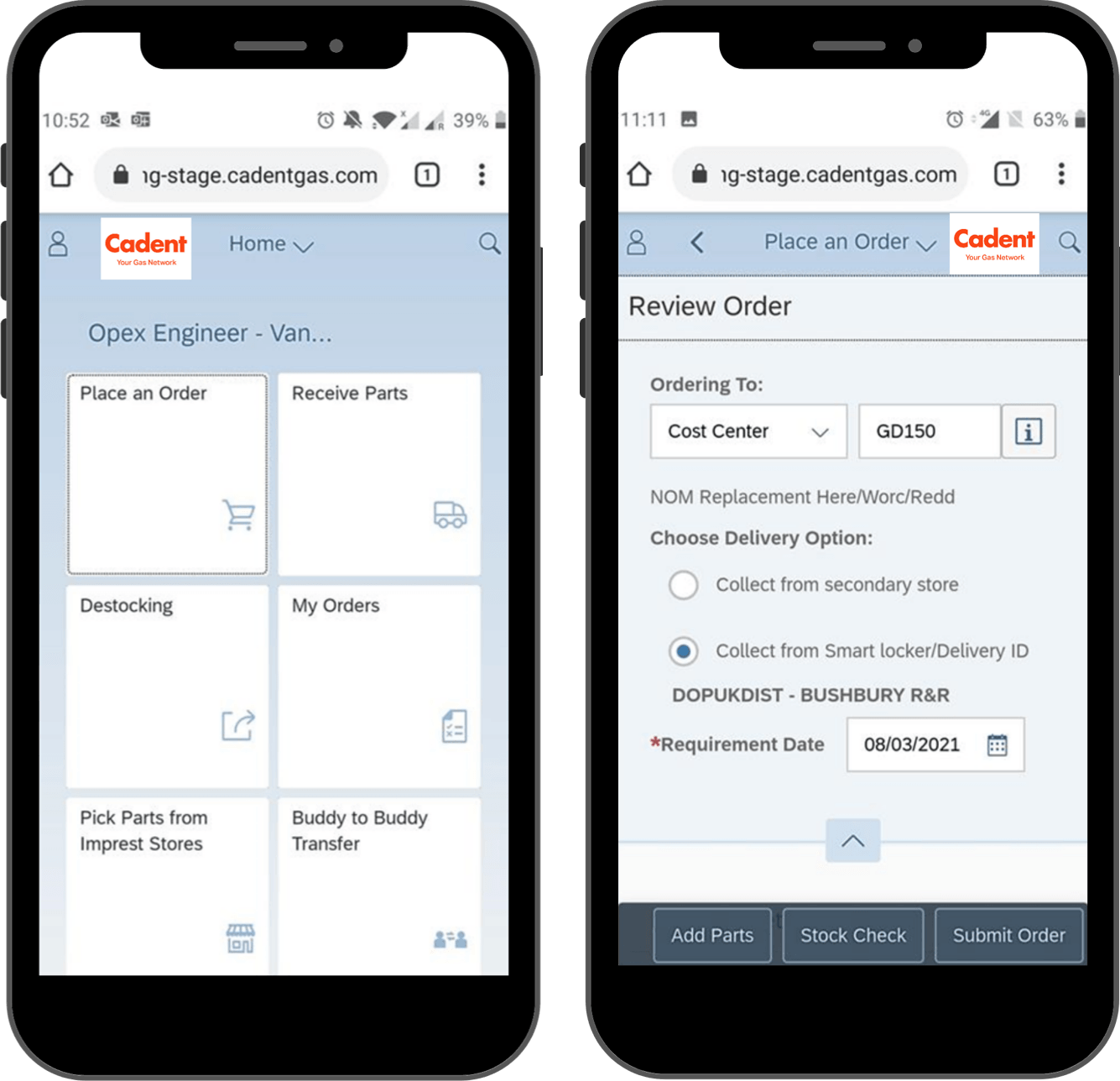
Rather than manually inputting part numbers from paper documents into a computer, staff in the warehouse can simply scan the parts’ barcodes and the details will automatically update in the SAP EWM system.
Field engineers can quickly and easily order parts to their nearest store, ensuring they have everything they need to respond to customers, streamlining the process of repairing the gas network and therefore reducing down time.
Benefits
Efficiency
Warehouse Management processes become more efficient, making employees more productive.
Customer satisfaction
Field engineers can quickly & easily order the parts they need, enabling them to provide better service, resulting in higher customer satisfaction
Business as usual
Solution was implemented without disrupting business as usual, by building a parallel SAP Template.