Are you looking to optimise the procurement and picking process for Dual Source parts from an EWM-managed warehouse?
Managing dual-source parts can be difficult in fixed bins in the warehouse. Additionally, storage and retrieval of parts from fixed bins can be challenging if the parts have multiple pack sizes. It can result in Partial picking and exception handling which impacts the overall efficiency and productivity of the warehouse.
This case study is to provide an overview of how to efficiently manage dual-source parts with multiple pack sizes in a warehouse fixed bin. This will ultimately make your supply chain more efficient, cost-effective and resilient.
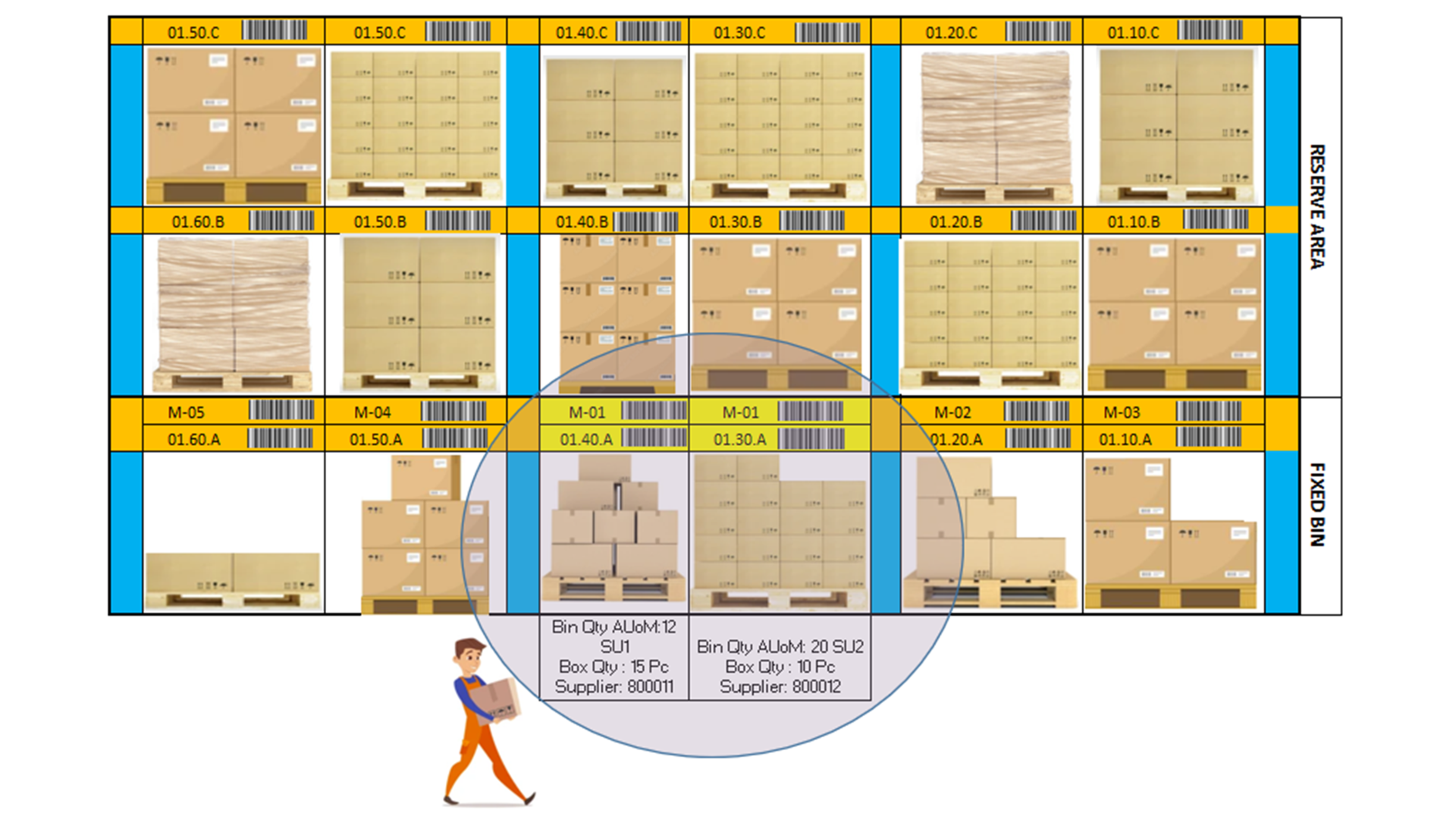
Process steps
Dual-source parts and different Pack sizes presents some challenges in the warehousing processes. All of these points must be considered for the process to go smoothly:
- Products are procured from more than one supplier
- Each supplier supplies products with different box quantity
- Products are received into Pallets and are stored in Rack storage in the Warehouse
- Replenishment is executed from Reserve Rack Storage to the fixed bin
- Handling units are not used in fixed bin storage, or Storage of nested Handling units can complicate the picking process from fixed Bin storage
- Picking is carried out from the fixed bin in the Warehouse
- Production Pick request quantity or the STO/Customer Outbound delivery quantity is not in multiples of box quantity
- Over-picking can be allowed within permissible tolerance limit to allow rounding of box quantity
Challenges
Dual Sourced parts have different box sizes, as they are specific to each supplier. This can cause below issues during MRP planning and Warehouse picking, if not managed correctly.
1. MRP is generating requirements based on quota and material master rounding Value. Procurement team to manually update Purchase order quantities based on supplier pack quantity (or box quantity).
2. Fixed Bin Storage does not store the box quantity. Warehouse pick quantity is not in multiples of box quantity. During picking execution, the picker picks the requested quantity following the below approach:
- The picker needs to physically open/break the box for picking partial quantities
Or
- Picker has to manually intervene and adjust the requested quantity by declaring exception during pick execution
Picking partial box quantity is not desirable as it requires counting which can slow down the picking process. Manually adjusting pick quantity to box quantity by picker the requires additional expertise and is recommended only in exceptional scenarios. Both approaches can result in human errors too.
These approaches have a significant impact on warehouse operations and the end-to-end supply chain.
3. Nested Handling units can be used as a possible solution for rounding the pick quantity to multiples of Box Handling units. However, this complicates the stock management of fixed bins. It requires additional labels at box level and an additional step during picking to confirm the box Handling unit to be picked.
4. The system does not store box quantities. Hence, it is difficult to track boxes in stock and round pick warehouse tasks in multiple box quantity.
How to optimise the process
These challenges can be overcome by automating the rounding of procurement quantity based on supplier pack factor during MRP run. Follow all the steps below to achieve optimisation of the process.
Master Data
Multiple fixed bins are assigned to products in EWM. Each fixed bin stores products with a different box quantity from each supplier. Mixing of stock with different Alternate Units of Measure is prohibited for the system, to ensure that the stock of different suppliers is not mixed. Boxes are represented with the Alternative Unit of measure in EWM rather than the Handling unit. Each Supplier has a specific box quantity which is stored in master data along with an Alternate Unit of measure for that supplier. Alternate unit to base unit conversion is also maintained in the material master.
Inbound
During the receiving process, the Inbound delivery quantity is converted from the ordering / Preferred unit to an Alternate unit of measure specific to a supplier. Handling units are created at the Pallet level. Putaway of the Handling units is carried out in the reserve area. Several boxes in the Handling unit can be seen in the Warehouse monitor (Quantity in Alternate Unit of measure in Physical stock). Physical Inventory can be done at box level using the Alternative Unit of measure.
Replenishment
Replenishment from the Reserve bin to the fixed bin is executed when the total stock at the fixed bin storage type level reduces below the minimum level. Full pallets are replenished from the Reserve storage type to the fixed bin storage type. Bins are replenished without mixing the stock. For example, if the bin consists of Boxes of size 10 PCs (AUoM – SU2), it gets replenished with Pallets with similar box size.
Outbound
Warehouse requests are created in EWM to pick products from EWM. The request can be created for Production supply, Customer sales orders, or Stock transports orders for another plant. Pick tasks are created from the fixed bin for the Warehouse request quantity. A fixed bin with the oldest stock is selected for picking (FIFO). Pick Warehouse tasks are rounded in multiple box quantities to avoid partial picking or opening of boxes. Rounding can result in over-picking of warehouse requests based on the allowed tolerance level. The picker will be presented with the Quantity in AUoM (number of boxes) to be picked from the fixed bin on the scanner. This will speed up the picking process and exception handling will no longer be required. The picker will pick the boxes and will go on to the next item for picking. Once all the products are picked and staged, the goods issue will be posted.
Conclusion
Dual sourced parts can be efficiently managed in Warehouse fixed bins by using multiple fixed bins. Supplier pack sizes can be mapped using the Alternative unit of measure, which will help to identify the pack size in the fixed bins. Rounding can further help to ensure that there are no partial boxes in the fixed bins.
Optimising this process will make your supply chain more efficient, resilient and cost-effective. If you'd like to learn more about how we can optimise your supply chain for your business needs, please get in touch.